-- Office of Research and Economic Development
Calendar Icon
Mar 14, 2013
Person Bust Icon
By Office of Research and Economic Development
RSS
Submit a Story
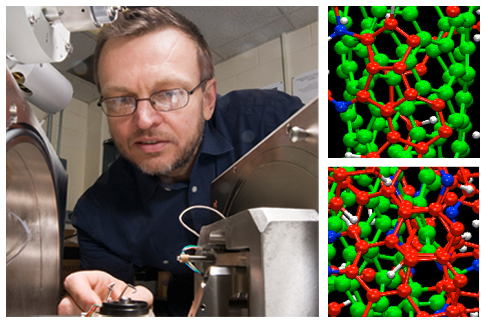
Carbon nanotubes, the super-strong building blocks of nanotechnology, hold the promise of reinforcing everything from golf clubs to airplane parts, but they’re difficult and expensive to process into something useful. University of Nebraska-Lincoln engineers have demonstrated a promising new way to exploit their unusual structure and properties more easily and less expensively.
The team, led by Yuris Dzenis, McBroom Professor of Mechanical and Materials Engineering, uses carbon nanotubes as a template to create a better carbon nanomaterial. They’re making continuous carbon nanofibers, which offer advantages over nanotubes alone in structural materials.
Their findings may prove a breakthrough in the next generation of carbon fiber composite materials, Dzenis said.
“Carbon nanotubes are really expensive still after two decades of development,” said Dzenis, a member of UNL’s Nebraska Center for Materials and Nanoscience. “There is a high interest in both utilization of their properties and reduction of costs, and there’s a possibility that, with what we’ve discovered, we may be able to produce high-quality, high-performance continuous nanofibers at low cost.”
Carbon fiber, the strongest commercially available structural material today, is a lightweight reinforcement used to strengthen polymer composites. Scientists seek to further strengthen advanced, high-performance fibers using exceptionally strong and fatigue-resistant carbon nanotubes, sheets of one-atom thick carbon molecules shaped into hollow cylinders. Their hexagonal honeycomb structure has special properties useful in nanotechnology. But nanotubes are short and expensive to make, and aligning enough of them properly to be commercially and economically feasible for use in structural materials has remained elusive.
To try to overcome these obstacles, scientists use a technique called electrospinning to produce continuous carbon nanofibers using carbon nanotubes.
Electrospinning involves applying high voltage to a polymer solution until a small jet of liquid ejects, resulting in limitless lengths of nanofibers. So far, these electrospun carbon nanofibers have been of poor quality.
Dzenis and colleagues think they have a solution. Using a small amount of well-placed double-walled carbon nanotubes, provided by collaborator MER Corp., to guide the formation and orientation of the nanocrystalline graphitic structure, they found they can use UNL-developed nanomanufacturing processes to create high-quality continuous carbon nanofibers.
Using in-situ scanning electron microscope experiments, collaborators at Northwestern University, led by Horacio Espinosa, confirmed the strength of the nanotube-nanofiber interface produced with using this process. Modeling by Northwestern’s George Schatz’s group provided insights into initial stages of the process.
In addition to significantly improving the structure and orientation in carbon nanofibers, the material has other advantages, Dzenis said. While still nano-sized for use in nanotechnology applications, nanofibers also can be created in limitless lengths to be more easily used in macroscopic materials and composites. Also important, the new fabrication process creates the greatest structural improvements at low temperatures, contributing to its potential low cost and ease in manufacturing.
“Significant improvements in structure at lower temperatures came as a surprise,” Dzenis said. By analyzing possible reasons for this, UNL researchers came up with an idea of a possible new mechanism for improving the system.
The UNL team is investigating this mechanism and continues to collaborate with Northwestern. “If further confirmed, this may lead to radically new ways to produce high-performance, ultra-strong carbon fibers,” he said.
The team published its findings in the American Chemical Society journal, ACS NANO. Dzenis’ co-authors are mechanical and materials engineering colleagues Dimitry Papkov, Alexander Goponenko and Yan Zou, who are affiliates of UNL’s Nebraska Center for Materials and Nanoscience; Allison M. Beese, Mohammad Naraghi, Horacio D. Espinosa, Biswajit Saha, George C. Schatz and SonBinh T. Nguyen of Northwestern University; and Alexander Moravsky and Raouf Loutfy of Materials and Electrochemical Research Corp., Tucson, Ariz.
This research was funded primarily by a U.S. Army Research Office Multidisciplinary University Research Initiative grant to the team led by Northwestern’s Espinosa in collaboration with researchers at UNL, MIT and MER Corp. The National Science Foundation and the Air Force Office of Scientific Research also helped fund this research.
The team, led by Yuris Dzenis, McBroom Professor of Mechanical and Materials Engineering, uses carbon nanotubes as a template to create a better carbon nanomaterial. They’re making continuous carbon nanofibers, which offer advantages over nanotubes alone in structural materials.
Their findings may prove a breakthrough in the next generation of carbon fiber composite materials, Dzenis said.
“Carbon nanotubes are really expensive still after two decades of development,” said Dzenis, a member of UNL’s Nebraska Center for Materials and Nanoscience. “There is a high interest in both utilization of their properties and reduction of costs, and there’s a possibility that, with what we’ve discovered, we may be able to produce high-quality, high-performance continuous nanofibers at low cost.”
Carbon fiber, the strongest commercially available structural material today, is a lightweight reinforcement used to strengthen polymer composites. Scientists seek to further strengthen advanced, high-performance fibers using exceptionally strong and fatigue-resistant carbon nanotubes, sheets of one-atom thick carbon molecules shaped into hollow cylinders. Their hexagonal honeycomb structure has special properties useful in nanotechnology. But nanotubes are short and expensive to make, and aligning enough of them properly to be commercially and economically feasible for use in structural materials has remained elusive.
To try to overcome these obstacles, scientists use a technique called electrospinning to produce continuous carbon nanofibers using carbon nanotubes.
Electrospinning involves applying high voltage to a polymer solution until a small jet of liquid ejects, resulting in limitless lengths of nanofibers. So far, these electrospun carbon nanofibers have been of poor quality.
Dzenis and colleagues think they have a solution. Using a small amount of well-placed double-walled carbon nanotubes, provided by collaborator MER Corp., to guide the formation and orientation of the nanocrystalline graphitic structure, they found they can use UNL-developed nanomanufacturing processes to create high-quality continuous carbon nanofibers.
Using in-situ scanning electron microscope experiments, collaborators at Northwestern University, led by Horacio Espinosa, confirmed the strength of the nanotube-nanofiber interface produced with using this process. Modeling by Northwestern’s George Schatz’s group provided insights into initial stages of the process.
In addition to significantly improving the structure and orientation in carbon nanofibers, the material has other advantages, Dzenis said. While still nano-sized for use in nanotechnology applications, nanofibers also can be created in limitless lengths to be more easily used in macroscopic materials and composites. Also important, the new fabrication process creates the greatest structural improvements at low temperatures, contributing to its potential low cost and ease in manufacturing.
“Significant improvements in structure at lower temperatures came as a surprise,” Dzenis said. By analyzing possible reasons for this, UNL researchers came up with an idea of a possible new mechanism for improving the system.
The UNL team is investigating this mechanism and continues to collaborate with Northwestern. “If further confirmed, this may lead to radically new ways to produce high-performance, ultra-strong carbon fibers,” he said.
The team published its findings in the American Chemical Society journal, ACS NANO. Dzenis’ co-authors are mechanical and materials engineering colleagues Dimitry Papkov, Alexander Goponenko and Yan Zou, who are affiliates of UNL’s Nebraska Center for Materials and Nanoscience; Allison M. Beese, Mohammad Naraghi, Horacio D. Espinosa, Biswajit Saha, George C. Schatz and SonBinh T. Nguyen of Northwestern University; and Alexander Moravsky and Raouf Loutfy of Materials and Electrochemical Research Corp., Tucson, Ariz.
This research was funded primarily by a U.S. Army Research Office Multidisciplinary University Research Initiative grant to the team led by Northwestern’s Espinosa in collaboration with researchers at UNL, MIT and MER Corp. The National Science Foundation and the Air Force Office of Scientific Research also helped fund this research.
Submit a Story